奔向世界的兴龙轮毂——河北省政府质量奖获奖单位秦皇岛兴龙轮毂有限公司质量发展纪实
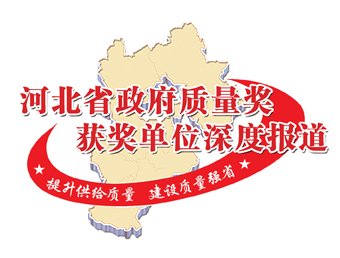
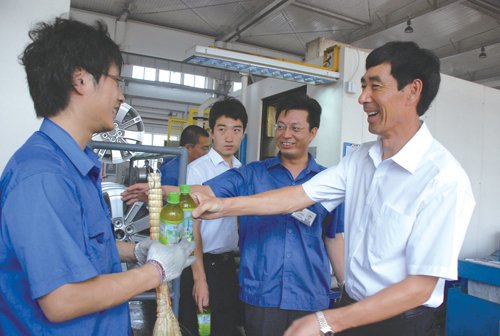
田纯刚慰问一线员工
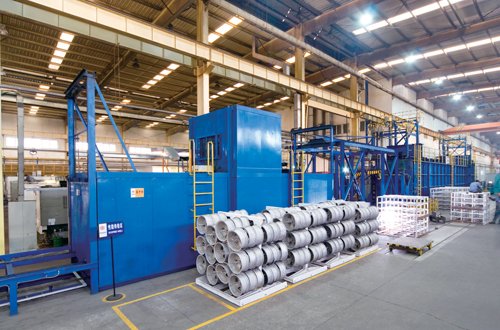
铸造-热处理
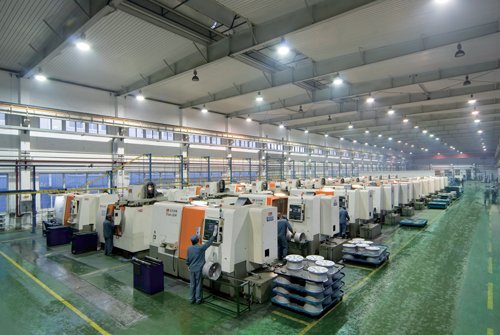
铸造-机加
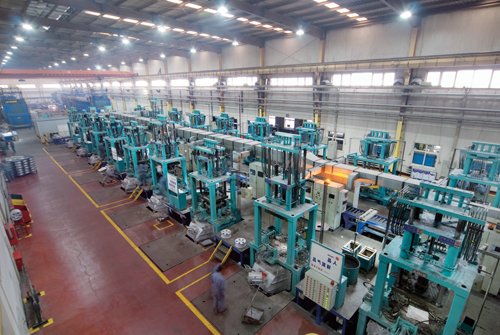
铸造-压铸
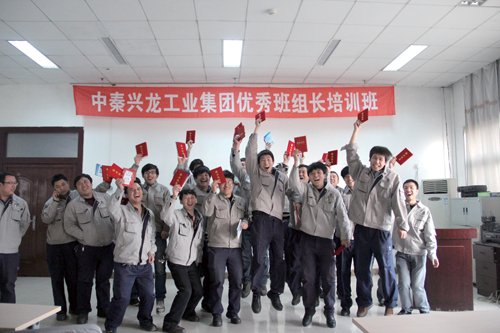
优秀班组长培训
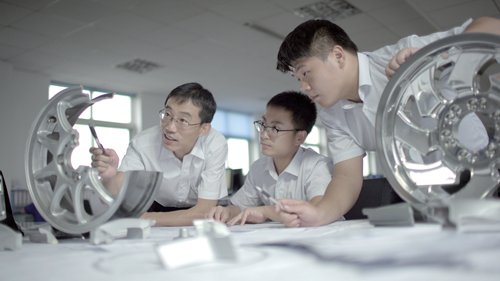
研发
8月中旬,一则“好消息”从地球的另一个半球传来,澳大利亚对原产于中国的铝制车轮作出反倾销和反补贴快速复审终裁:秦皇岛兴龙轮毂有限公司(以下简称兴龙轮毂)的倾销幅度和补贴率均为0,因此不对其加征反倾销税和反补贴税。“胜诉”的背后,是兴龙轮毂凭借着过硬的质量,正一步步成为一个奔向世界的轮毂品牌。
在港城,“兴龙”这个名字家喻户晓。作为一家专业从事铝合金汽车轮毂的研发制造型企业,兴龙轮毂是中秦兴龙投资控股有限公司的全资子公司。这家成立于2005年现在年仅“12岁”的企业,已经是一家集研发、生产、检测、销售、服务等于一体的高新技术企业,先后斩获省级高新技术企业、河北省著名商标、河北省质量效益型先进企业和省名牌产品、首届秦皇岛市政府质量奖等殊荣。现在,他们的荣誉簿上又加上了浓墨重彩的一笔——河北省政府质量奖。
说起公司快速成长的秘诀,兴龙“掌门人”田纯刚说得最多的就是质量。“我们始终坚持质量是企业生命的宗旨,把‘在汽车零部件产业成为国际知名供应商’作为企业长足发展的愿景,把‘精益求精’作为全员秉承的质量理念,推进全员精益改善与创新,激发员工的主动创新热情,营造全员创新氛围,‘向质量要产量,向质量要效益’,才有了今天的发展规模和势头。”田纯刚掷地有声地说到。
改进改善“提”质
熔炼是整个轮毂生产过程的第一道工序,铝液质量将直接影响产品的质量,而铝液精炼除气操作是保证铝液质量的重要环节之一,对去除铝液内氧化夹渣物及氢含量起着关键作用。
“精炼除气是通过变频可调节转速石墨转子将惰性气体氮气通入铝液中,旋转的石墨转子把通入铝液中的气体打散成微小气泡,并均匀扩散在铝液中,使铝液中的氢气不断扩散到惰性气体氮气气泡中,随着惰性气体氮气气泡上升浮到铝液表面,达到去除氢气的效果。”一边指着生产车间的生产线上的设备,兴龙轮毂制造部部长李宗保一边告诉记者,在实际生产过程中,石墨转子及挡渣板等配套设施为石墨材质,耐高温耐腐蚀效果差,且腐蚀过程中石墨粉卷入铝液存在夹渣风险,直接影响着铝液质量及压铸产品后续废品量,并且石墨转子的更换周期为一周左右,使用成本约2200元。
于是,为降低原材料成本消耗,兴龙轮毂的工人们进行自主改善,选用新型材料碳化硅材质转子及挡渣板,通过2个月的实验,转子及挡渣板无明显腐蚀受损,实验效果明显:不但每年可节约成本10.56万元,同时也可解决石墨转子使用过程石墨粉脱落所产生铝液夹渣问题,有效控制铝液质量,降低夹渣产生的废品率,为后序产品质量的提升起到促进作用。
无独有偶。在热加车间,2016年年初在质量方面成立降低漏气率精益小组,通过鱼骨图分析,找出要因,制定对策,漏气率2015年的平均1.7%降低到2016年5月份的0.57%;喷涂车间,2014年亮粉单耗为32克,超出公司指标110万元,车间在喷涂辅料方面的成本压力非常巨大。正是在这样的背景之下,2015年1月份车间迅速成立了降亮粉成本的QC小组,运用“柏拉图”分析,采用QC手法,小组成员经过6个月的努力,亮粉单耗降低至21克,共计节约成本约220万元;机加、热加车间,在效率方面成立快速换模、换型精益小组,通过以精益小组的形式进行工作开展,使用SMED方法,通过录视频、掐时间,将整体换型过程制作成作业票,区分内外作业,努力将内作业转换成外作业,优化内外作业时间,使用甘特图进行过程跟进,用折线图进行效果验证。热加快速换模由2015年的28分钟/次,降低到2016年1~5月份平均的19分钟/次……
“全员参加的持续改善活动,是我们质量提升强大生命力的源泉,是企业迅速发展的秘密。”李宗保说,兴龙轮毂一直秉承“持续改善、尽善尽美”的经营理念,持续的开展现场改善活动,不满足于现状,不断追求更高的附加价值,在提升质量、降低成本、效率提升等方面,取得了显著成效。
据介绍,兴龙轮毂自成立以来就以人为本不断推进全员精益改善与创新,激发员工的主动创新热情,营造全员创新氛围,在生产过程中借助精益生产推广,通过节拍优化、设备改造升级,不断提升自动化水平,实现效率逐年持续提升,过去3年通过基层员工的主动识别,在提高生产效率方面的自发性改善项目就达到1093项。以过程在制的控制方面为例,通过全员改善和工序间拉动,产品在制品周转时间由原来的45小时缩短为33小时,实现了同行业标杆水平。在工艺创新上,兴龙轮毂打破以往低压铸造全风冷技术模式的束缚,通过改进创新,积极摸索全新的低压铸造水雾冷和全水冷工艺,使S116、S117、S118产品不仅满足了日本VIA产品标准和客户质量要求,还实现了年增产7.8万件的开拓性成果。
“几年来,我们通过建立关键KPI指标、标杆数据对比分析,不断超越自我,超越标杆,用卓越的理念,追求卓越的结果。卓越绩效管理模式的推广,使得公司综合成品率、一次下线率、产量及交付等过程管理指标得到显著提升。”李宗保说。
2013年起,兴龙轮毂积极导入丰田精益生产管理理念,通过聘请日本丰田精益专家亲临现场进行问题会诊、理论培训、过程辅导,培养一批精益人才。此后3年兴龙轮毂大力推行全员精益改善,员工自发质量改善项目3922项。其中突出改善项目喷涂下线物流改造项目、自主研发并批量投产的压铸机械手项目、氦气机自动拔塞等项目,公司综合成品率和一次下线成品率均得到稳步提升。
创新驱动“升”质
“企业发展离不开竞争,作为参与国际化竞争的工厂,放眼未来,机遇与挑战并存,我们将技术资源作为公司战略核心部分,高度重视,特别是在引入并学习《卓越绩效评价准则》后,我们更加清晰地定位技术资源的作用与如何做创新和知识的积累。”说起技术创新对于质量提升的作用,兴龙轮毂技术部部长何平平一下子打开了话匣子,有着说不完的话题。
作为一家主打产品为OEM(贴牌加工)的企业,可能在很多人眼里缺乏技术含量,但在何平平看来,这是对OEM企业认识的一个误区甚至是误解。“在OEM市场上,我们通过持续深化与行业龙头戴卡集团的合作,以世界先进的产品标准与技术要求为目标,实现了以通用、福特、大众、日产为主的产品定位,主打高端市场;在零售产品上,实现了与日本、欧洲、美国改装市场客户同步研发的技术实力。”他一脸自豪地说道:“在质量控制过程中,我们坚持‘产品质量先期策划的事前控制,过程异常快速反应的事中控制,问题发生后根本原因查找的事后控制’原则,针对OEM产品大规模批量性和零售产品小批量、多品种的制造特点,全面开展质量管理创新。”
OEM产品与世界先进标准对标开展全面质量管理创新,自主产品则在创新方面不遗余力,实现了与日本、欧洲、美国改装市场客户同步研发的技术实力。说起企业在产品创新方面的“秘诀”,客户需求驱动成为何平平嘴里的一个高频词:“以客户需求为驱动方面,我们不断研究新技术、新工艺,3年开发了240余款新产品。”
据介绍,兴龙轮毂通过前期市场的广泛深入调查,根据不同顾客对产品的各种需求,对关键技术进行攻关、创新。通过长期的技术积累,目前兴龙轮毂的开发能力具备与整车厂同步研发的强大实力,可进行车轮2D与3D设计、性能分析、装配仿真、工艺模拟,开展车轮尺寸、冶金材料性能、可靠性与安全性、涂层性能等数十项试验检测,可生产12~24英寸不同大小的产品,同时具备对产品进行各种表面处理的能力,可生产全涂装工艺产品、精车工艺产品、镜面车工艺产品、抛光工艺产品、铣加工工艺产品、电镀银特殊漆工艺产品、套色工艺产品、拉丝工艺产品等不同工艺类型的产品。
尤为重要的是,兴龙轮毂坚持技术创新和质量提升双轮驱动,强化技术对质量的支撑。具体措施包括在新产品开发阶段,依据质量先期策划组织试生产,通过试生产摸索和制定合理的量产工艺;对关键过程控制点进行充分策划,对过程检验点进行有效管控,保证关键特性稳定、受控;提升技术人员能力水平,立足现场,合理制定工艺文件和产品控制标准,测算生产节拍,实现均衡生产,质保系统严格按标准进行现场检查,工艺变更严格按流程进行评审、验证,特殊情况下的技术工艺、标准降低权限上升至总工或总经理。目前,兴龙轮毂依托两个科技中心平台,深入开展车轮轻量节能新材料与新工艺、车轮制造新装备及成套技术、车轮大型化制造技术等方向的研究。与传统工艺相比,急冷工艺产品整体强度提高10~20%,轻盈系列产品减重可达7%,产品更加安全、耐用、节能、环保。
同时,兴龙轮毂为激励员工“万众创新”,专门建立了《合理化建议管理办法》《创新管理办法》《科技进步及成果转化奖励办法》《QC活动管理办法》等等各项制度以保证技术的发展,并按卓越绩效的理念进行推进,已经取得了良好的成绩。
毛坯冒口粘铝一直是兴龙轮毂所面对的技术难题。原来冒口粘铝不仅影响毛坯外观质量,形成大量废品流入后序,还在生产铸造过程中,需要大量的人力、物力来进行清铝操作,其中00614C23轮型冒口粘铝问题最为严重。
“00614C23轮型中心孔机加加工直径为57mm,浇口直径53mm,单边余量2mm。在铸造生产过程中冒口部位粘铝,操作清理频繁,并且产生大量废品流入后序,占比3%。”何平平解释说,“解决生产过程中毛坯冒口粘铝,可以有效保证生产节拍,更重要的是减少废品毛坯流入后续而造成不必要的经济损失。”
针对此类问题,兴龙轮毂制造部——热加序技术组于2016年12月启动冒口粘铝专项技术攻关,经过前期实地生产情况调查,热加序技术组商讨并制定了模具浇口套改进技术方案,并在重点轮型00614C23-M11X进行生产试验。
经过一季度的努力,兴龙轮毂制造部热加序技术组成功开发并使用了内藏式浇口套。“该技术有许多的创新点,包括解决冒口粘铝,保证外观质量,减轻操作手劳动强度;缓解冒口双层,保证质量;增强冒口部位冷却,为降低毛坯整体温度场提供条件,提高生产效率;同时增大了铝液补缩通道,减少生产过程冒口缩松问题等。”何平平透露,针对00614C23冒口粘铝问题实行的消除冒口粘铝内藏式浇口套创新,可以有效地提升00614C23班产效率5件,每月可多产出毛坯2200余件,增加经济效益2万余元。同时,每日可减少冒口粘铝及冒口缩松废品20余件,每月减少废毛坯600余件,减少经济损失3万余元,每年可创造有效经济价值63.1万元。与此同时,内藏式浇口套的应用已形成规范,现已普遍推广至05513C08以及05513C06等轮型实际生产中。
类似这样的技术创新提升质量的案例还有很多。“公司高层根据年度经营计划的完成情况和管理评审结果等及时作出战略调整,提出创新要求。各职能部门根据绩效指标评审情况,并结合战略调整要求制定系统的职能改进与创新计划和目标,主要从管理创新与技术创新两个方面进行。在公司制度的支持下,调动员工的创新积极性,并组织员工到行业内的轮毂厂参观学习,提高其创新能力;每月对合理化建议、创新项目进行评价并激励,每个季度将优秀项目上报集团参加集团创新项目做经验分享与评比,每年度做项目立项,并将项目过程与成效上报市、省参与科技成果鉴定。”何平平说,兴龙轮毂大力支持全体员工创新工作并将工作经验知识显性化。
据统计,兴龙轮毂目前共计获得专利36项,其中发明专利4项,实用新型32项,获得省、市级优秀QC小组称号17个,获得省科技成果项目9项。
战略系统“强”质
每当说起这两组数字时,兴龙轮毂质量部部长张雨总是难以掩饰自己的兴奋之情。这两组数字就是兴龙轮毂最近5年来在产能实现跨越性提升的同时,质量的核心指标之一“综合成品率”稳步上升,从92%提高到当前的94%的行业领先水平;其二“客户投诉率”指标方面,虽然客户的质量要求愈发严格,但兴龙轮毂仍实现了6个PPM的目标。
“6个PPM就是说每发货18万件产品,最多出现1次客户投诉,我们作为外观件的产品,这种控制难度可想而知。”张雨告诉记者,兴龙轮毂两大质量核心指标数据耀眼的背后,是兴龙轮毂坚持用质量战略引领、质量体系保障、质量文化升华的结果。
汽车行业作为国民经济的支柱产业之一,竞争十分激烈,作为参与国际化竞争的工厂,战略规划对企业发展的作用至关重要。“兴龙轮毂在五年战略规划,指导下,每年年终都会围绕车轮市场、安全管理、技术开发、质量管理、生产管理、设备管理、动力管理、信息管理、人力资源管理、财务管理、采购管理、物流管理、文化管理、行政管理等14大模块展开研讨,进行阶段性诊断和重点目标修正。”兴龙轮毂总经理王小虎透露,兴龙轮毂新的“十三五”规划明确了以管理和技术为核心,以健全安全生产管控体系为前提,以全方位的人才队伍建设为推动力,以确保核心资源安全为原则,全面深化质量管理,加快生产线自动化、信息化升级,提升技术研发和工艺控制水平,稳定并开拓车轮自主产品市场,严谨筹划新项目,积极拓展非车轮业务,实现整体健康可持续运营,成为行业内具有综合竞争优势的汽车零部件制造企业的公司发展总目标。
在张雨看来,质量战略已经融入了兴龙轮毂的发展战略之中,成为兴龙轮毂质量发展的“指南针”和“方向盘”。“我们质量战略引领的总目标是依托强有力的技术支撑和标准化,强化‘质量安全’重要性,评价和改善质量管理方式,夯实质量基础建设,完善质量条件,推行创新活动,达到行业领先质量水平,迈入全面质量管理(TQM)阶段。”张雨说。
在战略的引领下,兴龙轮毂还十分注重发挥质量体系的保障作用。虽然只有12年的发展历程,但在质量管理体系方面,兴龙轮毂却是“经历丰富”——2008年通过了ISO/TS16949质量管理体系认证、2013年积极导入丰田精益生产(TPS)管理理念、2014年成功导入卓越绩效管理模式……目前,兴龙轮毂在质量管理体系方面以《卓越绩效管理模式》作为方向引领,以ISO/TS16949质量管理体系为技术保障,实现质量管理工作的有序开展,充分利用国际、国内汽车厂的质量审核作为质量提升的机会,一方面拿到进入目标汽车厂的通行证,更为重要的是对先进的质量控制手段进行了消化和吸收,应用了潜在失效模式和后果分析、实验设计等方式进行产品质量的前期策划,应用了统计过程控制进行质量风险预先防控,应用了测量系统分析进行测量以保证测量的准确度和精确度。
说起兴龙轮毂在质量管理方面的“亮点”,张雨特意提到了兴龙轮毂的质量制度建设,比如设立质量例会制度;建立“质量安全”实行一票否决制,上升质量抱怨处理高度,形成针对抱怨的问责及处罚机制;按部门设定质量工作计划及目标纳入绩效考核,全员签订质量责任状,完善质量考核制度和修订岗位说明书;完善技术标准化、管理标准化工作和计量工作,将DQSB(快速反应模块)纳入分层审核,形成预防性管理等。而从2016年起,兴龙轮毂还实施两个重要的质量创新:一是设立质量“红线”控制质量风险;二是成立产品质量管理委员会,其中下设2个模块9个运行小组,从技术提升到设备保障,从过程预防到实物管控,系统性地提升产品质量。
华为老总任正非曾经说过,唯有文化才能生生不息。在质量文化方面,兴龙轮毂也开始注重质量文化建设,用文化的力量建立质量管理的可靠城墙。“文化是公司之魂,我们秉承‘仁和、诚信、务实、求新’的公司精神,明确提出了‘向质量要产量,向质量要效益’的战略方针并为此寻找方法,坚持不懈,展现了公司文化无限的生命力。”兴龙轮毂综合管理部谭建彪介绍。
现在,兴龙轮毂正继续加大对汽车零部件产业的投入,持续扩大产能和市场占有率,投资建设新的汽车底盘轻量化零件部项目,新的生产线将于2017年末相继建成投产。追求质量没有终点,年轻的兴龙轮毂正在汲取各种先进的质量理念和方法,努力成为一只“奔向世界的中国知名轮毂”。 (宋方义 王 越)